There is no denying that a warehouse can be a dangerous workplace. It’s paramount that
workplace safety is a priority for every business that operates a warehouse. With so much
that can go wrong, it’s always best to stay ahead of hazards and safety concerns. That’s why we felt it would be useful to provide an overview of everything that goes into creating a safe warehouse.
Warehouse Hazards
The first step in understanding warehouse safety is being aware of the safety hazards that
exist. Warehouses are a little different from ordinary workplaces in the sense that there are hazards that you might not find elsewhere. Here is a quick rundown of some of the
warehouse-specific safety hazards everyone should know about.
Forklifts
A warehouse is probably the most likely place you’ll find a forklift. While they are useful for
moving heavy items quickly, they are still motorized vehicles that can be dangerous if
operated without care. It’s essential that anyone who drives a forklift has been properly
trained and is certified to drive this type of vehicle. It’s also important to drive forklifts at an appropriate speed and far from large crowds of people. Finally, forklifts should go through daily inspections to ensure they are working properly and won’t malfunction in the middle of being used to perform warehouse work.
Conveyors
Like forklifts, conveyors are most common in warehouse settings and help to transport
items. One of the biggest concerns with conveyors is an employee having clothing or part
of their body getting entangled, which can easily lead to an injury. Therefore, employees
who work around conveyors should be dressed appropriately without any loose clothing or items on their person. There should also be a heightened level of awareness for anybody who works with conveyors to prevent potential mistakes and injuries.
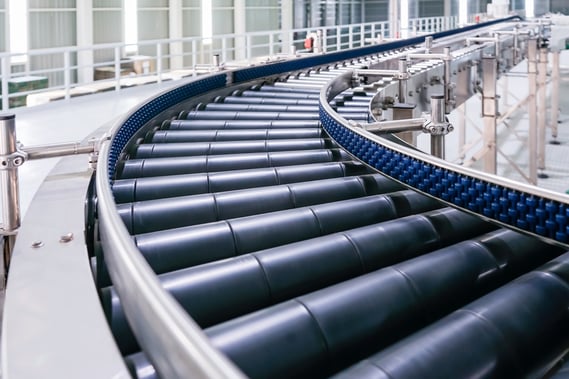
Chemicals
In some situations, warehouses store chemicals that can pose health and safety hazards.
Everyone who works with chemicals in a warehouse should be given proper training on
working with chemicals and only go near chemicals when they have the right personal
protective equipment. It’s critical that employees learn about the types of chemicals being
stored and how to properly store certain chemicals so that there is no chance
of contamination.
Following OSHA Standards
In terms of regulatory mandates, warehouses don’t have the strictest standards to follow.
Since they can be used in a variety of industries, they fall under OSHA’s general
requirements that apply to all workplaces. Nevertheless, those sometimes vague
standards must be upheld within a warehouse. Here are some of the OSHA standards that
warehouses need to keep in mind.
Hazard Communication
If there are hazardous substances within a warehouse, it’s required that businesses have a hazard communication program that’s written down and available for everyone. This
information must be accessible to all employees so that they can have a clear
understanding of the hazards that exist in the workplace and how to protect themselves.
Emergency Action Plan
In addition to sharing information about known hazards, warehouses also need to have a
plan in place in the event of an emergency. This plan is sometimes specific to fires, but it
can be applied to any emergency situation. Employees must know how to act and what to
do if there is a fire or an emergency that requires them to exit the building immediately.
Clear Exits
Speaking of exiting the building, this is also part of the standards that warehouses must
meet. According to OSHA, there must be two emergency exits in the warehouse that are
located as far apart as possible. This gives employees multiple exit points in case one is
blocked. It’s also required that these emergency exits are inspected regularly to check that
they remain clear of obstructions and that there is no other reason why employees
wouldn’t be able to use them in an emergency.
Fall Protection
Slips and falls are the most common type of safety accident in any workplace, but the
danger is even greater in a warehouse. There are multiple walking surfaces, employees
working at heights, and plenty of items that can be dropped and create a tripping hazard.
For employees who work at heights, specifically, warehouses must have a fall protection
system in place that can prevent the types of serious injuries that are possible if there is an
accident.
Warehouse Safety Tips
In a place like a warehouse, there is more to workplace safety than understanding hazards
or following regulations. It’s important to go the extra mile by making safety a top priority
and following good habits that can help to make everybody safe. Here are a few tips that
everyone who works in a warehouse should follow every day.
Guard Against Fire Hazards
As mentioned, there should be an emergency action plan in place in case there is a fire in a warehouse. Of course, fire prevention should also be a focal point for warehouses. In fact, OSHA requires a formal fire prevention plan for warehouses with at least 10 employees. This can be as simple as maintaining fire alarms, fire extinguishers, and a sprinkler system that can be used if there is a fire. Naturally, employees should be trained on how to use fire extinguishers and respond to fires appropriately. At the same time, employees should also be trained to recognize some of the potential causes of a fire in a warehouse and what steps they can take to prevent a fire from ever happening.
Handle Sharp Objects Safely
Sharp objects are among the most common hazards in a warehouse. Employees
frequently use knives to cut objects, although there are other objects found in a warehouse that are sharp enough to pierce skin. Employees who work with these types of objects should be trained on how to protect themselves. They should also be provided with gloves and other protective equipment that can offer protection. It also helps to train workers on how to use knives, scissors, or any other sharp objects that could potentially cause harm to themselves or someone else.
Practice Proper Ergonomics
It goes without saying that there is a lot of heavy lifting and carrying of objects in a
warehouse. This requires ergonomic training for all employees. They need to be instructed
on how to lift items in a safe manner that limits the strain on their body and prevents
skeletal-muscular injuries. Keep in mind that ergonomics isn’t just about preventing short-term injuries. Practicing proper ergonomics can also prevent injuries that might show up in the future.
Create Signs for Hazardous Areas
Something as simple as posting signs can make a big difference when it comes to warehouse safety. After all, not all parts of a warehouse are the same; some are more dangerous than others. If there are chemicals being stored or dangerous equipment being used, those are areas where personnel should be limited. Therefore, it’s best to post signs that warn of dangers in a specific area, telling employees that they should not be in those areas unless they have work to perform there. In fact, labeling tools, equipment, and anything else in a warehouse can have a similar effect, helping keep people aware of dangerous areas and items.
Proper Clothing and PPE
The use of personal protective equipment is huge for warehouse safety. Workers
performing specific types of jobs need to be wearing proper clothing for those tasks and have safety equipment that’s appropriate. Depending on the job, employees may require hard hats, eye protection, vests, gloves, or other equipment. Typically, loose-fitting clothes are a problem waiting to happen with some of the machinery found in warehouses. It can also be a good idea to have all employees wear high-visibility clothing to add an extra degree of safety.
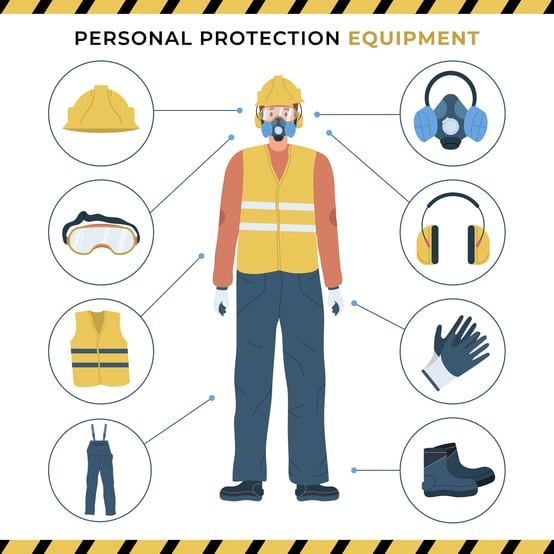
Proper Ventilation
Good ventilation is a safety measure that sometimes gets overlooked in warehouses. In
certain areas of a warehouse, air circulation could be limited, which is particularly
dangerous if there is vehicle exhaust or other fumes in the air. Warehouses need to use
exhaust fans and the building’s HVAC system to ensure there is proper circulation and air
quality. The same can be said of controlling the temperature and humidity inside the
warehouse so that employees aren’t subjected to unsafe working conditions.
Keep the Floor Clear
In a warehouse, a clean floor is a virtual necessity. It’s already dangerous enough working
in a warehouse without adding slippery floors or loose debris to the equation. These types
of hazards add to the chances that someone could trip and fall, leading to an injury. The
good news is that these types of hazards are fully preventable. The key is preaching to
employees the importance of keeping floors and walkways clear of debris and making sure
workers understand the importance of this from a safety perspective.
Maintain Safety Records
Last but not least, it’s always a good idea for warehouses to maintain a record of all safety-
related activities. This includes a log of accidents, both big and small, as well as a record of
safety inspections and maintenance. By keeping a record of this information, it’s easier to
spot patterns or shortcomings as they relate to warehouse safety. This allows companies
to find areas where safety can be improved and make informed decisions about how to
improve safety. The more information available about safety in the workplace, the easier it
is to make decisions that can help improve safety in the workplace.
