For countless companies, winter can complicate their ordinary health and safety measures. The days are shorter, temperatures are colder, and winter weather can sometimes be unforgiving. Managing workplace health and safety is already challenging enough without adding winter into the equation. This makes the task of workplace health and safety even greater yet more important.
The best solution to this is utilizing proper EHS software to help manage every element of environmental, health, and safety in the workplace. The ability to stay organized is critical for businesses, especially with the extra challenges winter brings. Let’s take a closer look at the extra safety measures that can be taken during the winter months and the ways that EHS software can help any business manage those season-specific risks in addition to all of the other health and safety challenges they must take on all year round.
Seasonal Job Hazard Analysis
Conducting a proper job hazard analysis is one of the best ways to understand health and safety risks. This type of analysis can take stock of the seriousness of every workplace hazard and shine a light on what can be done to keep employees safe. Before winter arrives, it can be a good idea to conduct a seasonal job hazard analysis on how certain jobs could be changed and what seasonal risks will suddenly show up that weren’t there before. This is the best way for businesses to be aware of season-specific risks.
Keep in mind that American workplaces endure tens of thousands of workplace injuries and illnesses that are related to winter weather conditions in one way or another. There could be leaks in the roof, clogged gutters, slippery surfaces, or even new electrical hazards that pop up during the winter months. Every workplace needs to know which of these hazards could be present and what steps need to be taken to protect employees from them. There is a strong chance that something in every workplace will be different during the winter, so a winter-specific job hazard analysis is a good first step in managing those risks.
Extra Training
There is no such thing as too much safety training. This is especially true if there are additional safety concerns during the winter. After performing a job hazard analysis with a special focus on wintry conditions, extra safety training for employees is usually a good idea. After all, there is no point in discovering new safety threats if that information isn’t shared with employees. New safety hazards will likely change safety protocols that employees should follow or change how workers focus their energy and attention as it relates to safety.
Don’t forget that there could be certain types of equipment that are only used during the winter. Employees need to receive training on equipment and machinery that’s needed during the winter. Even if employees have used those tools before, if it’s been several months since they last used them, it’s best to train them again. The same logic applies to other types of workplace safety training that are only relevant during the winter.
Emergency Preparedness
Preparing employees for workplace emergencies is important 12 months of the year. However, the winter sometimes adds a new wrinkle to this. Wintry conditions can sometimes change the likelihood of a specific emergency taking place. There could also be winter-specific emergency scenarios that aren’t a concern for the rest of the year.
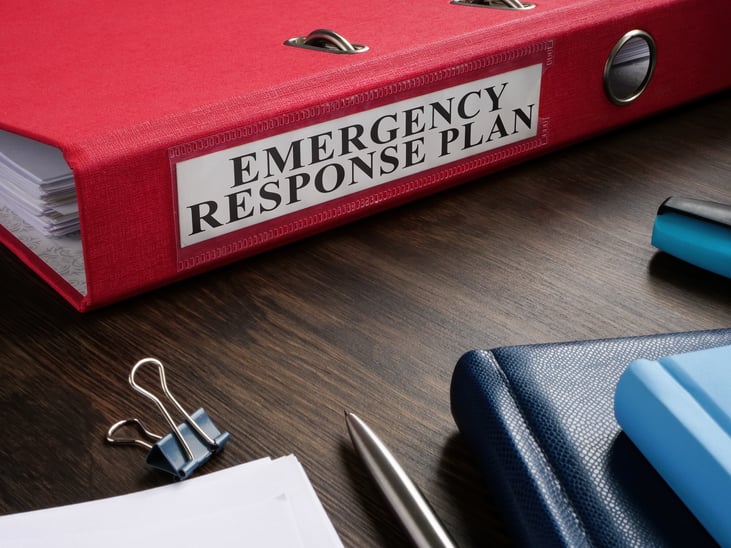
Therefore, safety leaders need to prepare for potential wintertime emergencies. Is it possible that emergency exits or evacuation routes could be impacted by winter weather? If one option is blocked or unavailable because of the weather, what is the next step for employees? Likewise, the tools and equipment employees might need in an emergency could change during the winter. For instance, if they have to exit the building, they will need to bring warm clothing with them during the winter. Much like some of the safety protocols and training exercises, there are bound to be differences in how emergency scenarios play out during the winter, so employees need to learn about these differences before winter arrives.
Vehicle and Driving Safety
There is a lot that can be said about how driving changes during the winter. Any business that has employees on the road driving company-owned vehicles to perform work should be proactive in promoting safe winter driving. In fact, any business that has employees who drive to work should make sure employees have a good understanding of how to drive in the winter.
Some safety guidelines might be obvious, but in the interest of safety, they need to be repeated. Ideally, the business should have protocols for how employees should drive in adverse conditions. There should be clear protocols for when it’s safe to drive and when it’s not safe to drive. Companies also need to be proactive in making sure their vehicles have been inspected and are ready to handle winter driving.
PPE Needs
A company’s PPE needs tend to change during the winter months along with everything else. If employees are required to work outside, they will need extra layers of clothing, not to mention hats, gloves, and perhaps eye protection as well. Businesses need to make sure they are well-stocked with proper wintertime PPE before the cold weather arrives. They also need to discuss changes to PPE protocols with employees before the weather turns. Keep in mind that employees might need some time to adjust to the new PPE needs and become comfortable working with new equipment and extra layers of clothing.

Lack of Daylight
During the winter, the weather will fluctuate, but the lack of daylight is one thing that can be predicted. Companies that require employees to work outside should know about the challenges of working in low light. They should also be able to plan ahead to maximize the time workers are outside while the sun is out. No matter the industry, working after dark is always going to be a little more dangerous. But there is no reason why businesses can’t be prepared and avoid putting employees in a difficult position.
Indoor Air Quality
On the other side of the coin, companies that operate indoors need to stay focused on air quality during the winter months. If it’s cold outside, employees can’t open windows to improve air circulation. Employers also have to rely on their HVAC system to pump heat into the building. This opens the door to air quality issues, including the presence of carbon monoxide, radon, and other dangerous gases. It’s critical to be proactive during the winter by testing the HVAC system and the air quality. Keep in mind that indoor, sedentary jobs aren’t completely out of the woods when it comes to winter-specific health risks.
Be Alert to Seasonal Illnesses
Whether employees are working inside or outside, seasonal illnesses during the winter are a concern. Employees will be more exposed to germs and illnesses like the flu or the common cold throughout the winter. If an employee gets sick and comes to work, the disease can spread quickly, leading to a lot of sick employees and workplace absences, neither of which is good for anybody.
Part of preparing for winter is reminding employees how to take care of themselves. Tell them to get plenty of rest, keep themselves hydrated, and proper hygiene protocols that can reduce the spread of germs. It’s also a good idea to encourage employees who are feeling sick to stay home so that they don’t risk infecting their co-workers. In the long run, one person should miss one day of work rather than spread germs that cause five other people to get sick, which is why employers need to do their best to stay ahead of season illnesses.
Regular Toolbox Talks
If there is one prevailing theme in preparing for winter from a safety standpoint, it’s training and communication. Holding daily toolbox talks can be an important part of winter preparation and wintertime workplace safety. There are a lot of changes that come in the winter, more than can be covered in a single training session or toolbox talk. By holding regular toolbox talks with employees, it’s possible to remind them of all of the new safety challenges and changes in protocol that are necessary during the winter. This can go a long way in preparing employees for the seasonal risks that winter brings.
Role of EHS Software
If the goal of a company is to be prepared for the health and safety challenges of winter, EHS software should be considered an essential tool. A top-notch health and safety management system can help with the countless challenges the winter brings. It can help to create winter-specific checklists related to safety, report new workplace safety hazards, schedule safety meetings, and track how much time employees spend outside exposed to cold weather.
With EHS software, it’s even possible to monitor the weather in real time. This allows decisions to be made about how to adjust outdoor work schedules and whether or not it’s safe to have vehicles on the road. There is perhaps no better tool for making decisions on the fly that are in the interest of employee safety. Obviously, it’s impossible to eliminate many of the safety hazards winter weather can create. But with EHS software, companies can manage the risks of winter-related accidents and injuries much more effectively.
