Environmental, Health, and Safety (EHS) compliance audits are crucial for any organization that wants to operate safely and responsibly. These audits help identify areas where practices might not align with regulations or internal policies. By proactively addressing non-conformities, organizations can minimize risks, prevent incidents, and ensure a healthy and sustainable work environment.
This article provides guidance on conducting successful EHS compliance audits and effectively addressing any identified non-conformities.
Planning and Preparation
The planning and preparation stage is the cornerstone of a successful EHS compliance audit. Here’s a detailed breakdown of this crucial step:
1. Define the Scope
- Risk Assessment: Conduct a comprehensive risk assessment to identify areas with the highest potential for non-conformities. Analyze factors like past incidents, near misses, specific processes, and regulatory focus areas.
- Compliance Requirements: Review relevant federal, state, and local environmental, health, and safety regulations that apply to your organization’s operations.
- Internal Policies: Consider including internal EHS policies, procedures, and safe work practices in the audit scope.
2. Assemble an Audit Team
- Competency: Select team members with the necessary expertise in EHS regulations, relevant industry standards, and auditing methodologies. Consider including personnel from various departments to gain diverse perspectives.
- Independence: The audit team should be independent of the areas being audited to ensure objectivity and unbiased findings.
- Training: Provide auditors with proper training on relevant EHS regulations, auditing procedures, and effective communication techniques.
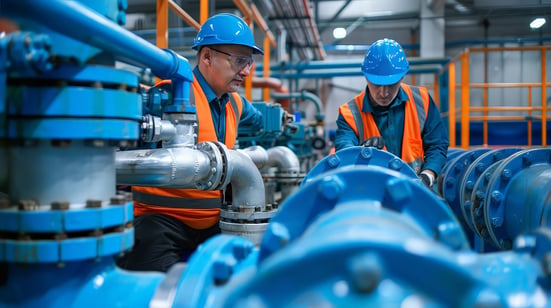
3. Develop an Audit Plan
- Objectives: Clearly define the specific objectives of the audit. These might include verifying compliance with regulations, evaluating the effectiveness of EHS programs, or identifying opportunities for improvement.
- Methodology: Outline the methods used to conduct the audit, such as document review, site inspections, and employee interviews.
- Schedule: Develop a detailed schedule for the audit, outlining the duration of activities, timelines for document review, site inspections, and reporting.
- Documentation Requirements: Specify the types of documents and records to be collected and reviewed during the audit.
- Resources: Identify the resources required for the audit, including personnel, equipment, and budget allocation.
4. Gather Information
- Regulatory Requirements: Collect all applicable environmental regulations, occupational safety and health standards (OSHA standards), and any industry-specific codes that govern your operations.
- Safety Data Sheets (SDS): Ensure access to current SDS for all hazardous materials used in the workplace.
- Previous Audit Reports: Review findings and corrective actions from past internal or external audits to identify recurring issues and track progress made.
- Operational Documents: Gather process flowcharts, operating procedures, emergency response plans, and other documents relevant to EHS practices.
By meticulously planning and preparing for your EHS compliance audit, you set the stage for a smooth and effective assessment. A well-defined scope, a competent audit team, a comprehensive plan, and readily available information will all contribute to uncovering non-conformities and ultimately fostering a safer and more compliant work environment.
Conducting the Audit
The audit itself is where the planning and preparation culminate in a detailed examination of your EHS practices. Here’s a breakdown of this crucial stage:
1. Document Review
- Compliance Manuals: Thoroughly examine environmental permits, safety manuals, and other documents outlining EHS policies and procedures. Ensure these documents are current, accessible to employees, and align with relevant regulations.
- Training Records: Review employee training records to verify completion of mandatory EHS training programs.
- Operating Procedures: Scrutinize standard operating procedures (SOPs) for hazardous materials handling, waste management, and emergency response procedures to ensure they are followed and effective.
- Maintenance Records: Evaluate maintenance records for equipment and safety features to verify they are up-to-date and functioning properly.
- Incident Reports: Analyze past incident reports to identify trends, root causes, and the effectiveness of corrective actions taken.
2. Site Inspections
- Visual Walk-Throughs: Conduct comprehensive visual inspections of workplaces, including production areas, storage facilities, and waste management zones. Look for potential hazards like improper chemical storage, housekeeping issues, or malfunctioning safety equipment.
- Equipment Verification: Verify that safety equipment like eyewash stations, fire extinguishers, and personal protective equipment (PPE) are readily available, properly maintained, and in good working order.
- Waste Management: Inspect waste storage areas and disposal practices to ensure compliance with environmental regulations.
3. Interviews
- Employees: Conduct interviews with employees at all levels to assess their understanding of EHS policies and procedures. Ask about safety concerns, near misses, and their comfort level reporting incidents.
- Supervisors: Interview supervisors to evaluate their role in enforcing EHS practices, conducting safety briefings, and addressing employee concerns.
- Management: Interview management to gauge their commitment to EHS compliance, resource allocation for EHS programs, and their overall safety culture.
Effective Communication
Throughout the audit process, maintain clear and open communication with all involved. Explain the purpose of the audit, answer questions openly, and actively listen to employee concerns. This fosters a collaborative environment and encourages transparency.
By conducting a meticulous document review, thorough site inspections, and insightful interviews, the audit team can gather a comprehensive picture of your EHS practices. This information is then used to identify non-conformities and pave the way for corrective actions in the following stages of the audit process.
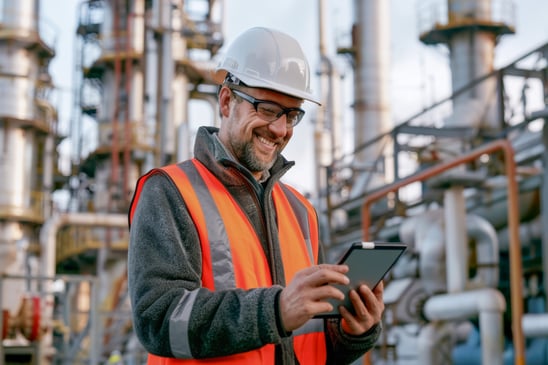
Addressing Non-Conformities
Identifying non-conformities during an EHS compliance audit is just the first step. The true value lies in effectively addressing them to prevent future occurrences and ensure continuous improvement in your EHS program. Here’s a breakdown of this crucial stage:
1. Identification and Documentation
- Clarity is Key: Clearly define and document all identified non-conformities. This includes a detailed description of the non-compliance, its location, and the relevant regulation or internal policy that was not followed.
- Severity Ranking: Categorize non-conformities based on their severity. This could range from minor deviations like missing safety data sheets to major concerns like malfunctioning safety equipment. Prioritize corrective actions based on this ranking.
2. Root Cause Analysis
- Digging Deeper: Don’t settle for simply identifying the non-conformity. Conduct a thorough root cause analysis to understand the underlying factors that led to the deviation. This might involve using techniques like the “5 Whys” method to ask a series of “why” questions to uncover the root cause of the issue. By identifying the root cause (unclear procedures), you can address the core issue and prevent future occurrences.
3. Corrective Action Plan (CAP)
- Charting the Course: Develop a comprehensive Corrective Action Plan (CAP) to address each identified non-conformity. The CAP should outline specific actions to be taken, timelines for completion, and individuals assigned with the responsibility of implementing the corrective actions.
- Specificity Matters: The CAP should be specific, measurable, achievable, relevant, and time-bound (SMART) to ensure effective implementation.
- Resource Allocation: Allocate necessary resources, including personnel, budget, and equipment, to successfully implement the corrective actions outlined in the CAP.
4. Verification and Follow-Up
- Closing the Loop: Don’t let the CAP gather dust. Implement a system for monitoring and verifying the effectiveness of corrective actions. This might involve follow-up audits, performance reviews, or data analysis to ensure the non-conformity has been truly addressed.
- Continuous Improvement: Utilize the findings from the audit and the corrective actions taken as opportunities to continuously improve your EHS program. Update procedures, enhance training programs, and refine your safety culture based on the learnings from the audit process.
By following a structured approach to addressing non-conformities, you can transform audit findings into a positive force for strengthening your EHS program and fostering a safer work environment.
Additional Tips
- Communication: Maintain open communication throughout the audit process. Inform employees about the audit’s purpose, findings, and corrective actions.
- Management Commitment: Demonstrate strong management commitment to EHS compliance. Allocate necessary resources and actively participate in the audit process.
- Continuous Improvement: Utilize audit findings to continuously improve EHS practices and procedures. Regularly review and update your EHS management system.
A Proactive Approach to Safety and Compliance
EHS compliance audits are not simply a box-checking exercise. They are a powerful tool for organizations to proactively identify and address gaps in their environmental, health, and safety practices. By following the guidance outlined in this article, you can conduct successful EHS compliance audits that:
- Minimize Risks: Identifying and addressing non-conformities before they lead to incidents helps prevent accidents, injuries, and environmental damage.
- Enhance Compliance: A strong audit program ensures your organization remains up-to-date with evolving regulations and minimizes the risk of regulatory fines or penalties.
- Foster a Culture of Safety: Regular audits demonstrate management’s commitment to safety and encourage a culture where employees actively participate in identifying and reporting potential hazards.
- Promote Continuous Improvement: The audit process provides valuable insights into your EHS program’s effectiveness. Utilize these learnings to refine procedures, enhance training programs, and continuously improve your overall safety culture.
Overall, investing in a well-planned and executed EHS compliance audit program is an investment in the safety and well-being of your employees, the environment, and your organization’s overall success. By proactively addressing non-conformities and fostering a culture of safety, you can create a sustainable foundation for a thriving and responsible organization.
