In today’s workplace, prioritizing the Environment, Health, and Safety (EHS) of employees and the surrounding environment is no longer optional. It’s a fundamental responsibility for organizations of all sizes. EHS management systems encompass a variety of practices and procedures designed to create a safe and healthy work environment, minimize environmental impact, and comply with relevant regulations. But how do you effectively identify and address the potential hazards that threaten these goals?
This is where risk assessment comes in. It’s a critical cornerstone of any successful EHS program, serving as a proactive approach to safeguarding your people, your assets, and the environment. Imagine a construction site. Just by looking at it, you can identify some potential dangers – heights, heavy machinery, and electrical hazards. But a thorough risk assessment would delve much deeper. It would consider not only the obvious hazards, but also less apparent ones like ergonomic risks associated with repetitive motions, exposure to dust and fumes, and potential weather hazards. By systematically examining all aspects of the workplace, risk assessment helps organizations uncover hidden dangers and prevent incidents before they happen.
What is a Risk Assessment?
Risk assessment is a systematic, multi-step process used to identify potential hazards, analyze the likelihood of their occurrence, and assess the severity of the consequences. It’s essentially a proactive approach to safeguarding your workplace environment, health, and safety. Here’s a breakdown of the key steps involved:
- Hazard Identification: This involves actively searching for anything in the workplace that could cause harm to people, property, or the environment. This can include physical hazards (e.g., slippery surfaces, falling objects, loud noises), chemical hazards (e.g., toxic materials, flammable liquids), biological hazards (e.g., bacteria, viruses), ergonomic hazards (e.g., repetitive movements, awkward postures), and psychosocial hazards (e.g., stress, bullying).
- Risk Analysis: Once hazards are identified, the likelihood of them occurring (probability) and the potential severity of the consequences (impact) are evaluated. This can be done qualitatively (descriptive terms like “high,” “medium,” “low”) or quantitatively (using numerical values). There are various risk assessment tools and matrices available to assist in this analysis.
- Risk Evaluation: After analyzing the probability and impact of each hazard, the overall level of risk is determined. High-risk hazards require immediate attention and implementation of control measures. Lower-risk hazards may still warrant preventative actions but can be addressed based on available resources and priorities.
- Risk Control: The aim is to minimize the likelihood and/or impact of identified risks. There are different risk control strategies, such as:
- Elimination: Completely removing the hazard from the workplace is the most effective control measure, but not always feasible.
- Substitution: Replacing a hazardous material or process with a safer alternative.
- Engineering Controls: Implementing physical changes to the workplace or equipment to reduce exposure to hazards (e.g., installing ventilation systems, machine guards).
- Administrative Controls: Establishing policies, procedures, and safe work practices to minimize risks (e.g., training programs, permit systems).
- Personal Protective Equipment (PPE): Providing appropriate PPE (e.g., gloves, goggles, respirators) to protect workers when other controls are not feasible.
- Documentation and Monitoring: The entire risk assessment process should be documented for future reference and to demonstrate compliance with regulations. Regular monitoring is crucial to ensure the effectiveness of implemented controls and to identify any new hazards that may arise.
By following these steps, organizations can gain a comprehensive understanding of potential workplace risks and take proactive measures to prevent accidents, injuries, and illnesses.
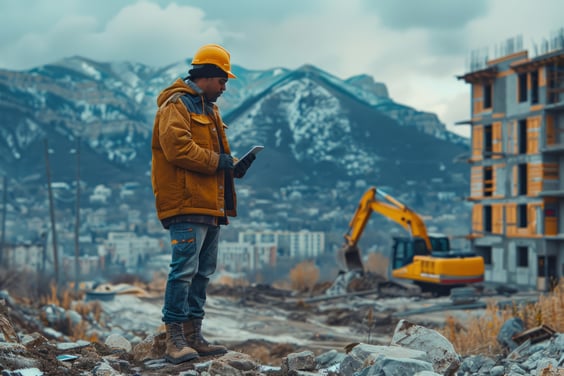
Why is Risk Assessment Important in EHS Management?
Risk assessment serves as the foundation for a proactive and successful EHS program. Here’s a deeper dive into the reasons why it’s essential:
- Increased Safety Awareness: A thorough risk assessment goes beyond simply identifying hazards. It delves into the “how” and “why” of potential incidents. This detailed analysis raises awareness among employees and management about:
- The specific dangers present in their work environment.
- The potential consequences of unsafe actions or procedures.
- The importance of following established safety protocols.
This heightened awareness fosters a culture of safety where everyone takes responsibility for preventing accidents and injuries. Employees become more engaged in identifying and reporting hazards, and management can tailor safety training programs to address specific workplace risks.
- Prioritization of Resources: Limited resources are a reality for most organizations. Risk assessments help prioritize which hazards pose the greatest threat based on the likelihood of occurrence and potential severity. This allows for the strategic allocation of resources towards:
- Implementing effective control measures for high-risk hazards.
- Developing targeted training programs for high-risk tasks or procedures.
- Investing in personal protective equipment (PPE) for essential protection against identified hazards.
By focusing on the most critical risks first, organizations can maximize the effectiveness of their EHS programs and achieve the greatest safety improvements.
- Compliance with Regulations: Many EHS regulations mandate that organizations conduct risk assessments for specific activities or processes. This includes standards set by OSHA (Occupational Safety and Health Administration) and the EPA (Environmental Protection Agency). Properly documented risk assessments demonstrate compliance with these regulations and can help organizations avoid:
- Hefty fines for non-compliance.
- Legal repercussions in the event of an accident or environmental incident.
Furthermore, a well-established risk assessment process positions organizations favorably during safety audits and inspections by regulatory agencies.
- Reduced Costs: The financial benefits of risk assessment are significant. By preventing accidents and injuries, organizations can dramatically reduce costs associated with:
- Medical treatment for work-related injuries and illnesses.
- Lost productivity due to employee absences.
- Workers’ compensation claims.
- Damage to property or equipment from accidents.
Additionally, proactive risk management can help minimize the risk of environmental damage and associated cleanup costs, potential fines, and reputational harm.
- Improved Decision-Making: Data gathered through risk assessments provides valuable insights to inform critical EHS decisions, such as:
- Selection of safe work practices for various tasks and procedures.
- Identification of the need for engineering controls to eliminate or minimize hazards at the source.
- Selection of appropriate personal protective equipment (PPE) to protect workers from residual risks.
Risk assessments also play a role in:
- Developing emergency response plans to effectively address potential incidents.
- Allocating resources for preventive maintenance programs to reduce the risk of equipment failure.
By basing decisions on a comprehensive understanding of workplace risks, organizations can create a safer and healthier work environment for employees and minimize the potential for costly accidents and environmental damage.
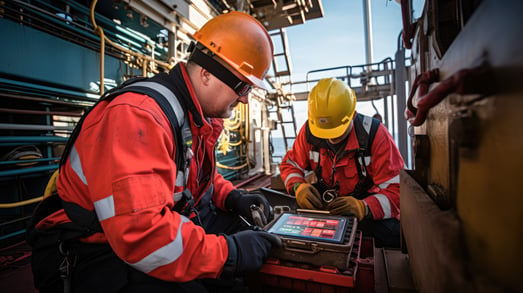
The Last Word on Risk Assessment
Risk assessment is not a one-time event; it’s an ongoing process that must adapt to dynamic workplaces. Regular risk assessments are essential to account for several factors, including:
- Changes in Operations: As production processes evolve, new equipment is introduced or work methods are modified. This means new hazards may emerge. Regular risk assessments ensure these potential dangers are identified and addressed before incidents occur.
- Introduction of New Equipment: New machinery or technology can introduce unforeseen risks. Integrating risk assessments into the procurement and implementation process for new equipment helps ensure its safe operation.
- Evolving Regulations: Regulatory requirements may change over time. Regular risk assessments help organizations stay up-to-date with compliance obligations and adapt their EHS programs accordingly.
By consistently evaluating and mitigating risks, organizations can achieve several key goals:
- Create a Culture of Safety: A proactive approach to risk assessment fosters a culture of safety where everyone is invested in preventing accidents and injuries. Employees become more aware of their surroundings and actively participate in safety initiatives.
- Minimize Environmental Impact: By identifying and controlling hazards that could harm the environment, organizations can minimize their ecological footprint and contribute to a more sustainable future.
- Achieve Overall EHS Goals: Risk assessment serves as the cornerstone of a successful EHS program. By systematically identifying and addressing workplace risks, organizations can create a safer and healthier work environment for employees, comply with regulations, and ultimately achieve their overall environmental, health, and safety goals.
Incorporating a robust risk assessment process into your EHS program is an investment in the well-being of your employees, the environment, and the long-term success of your organization.
