The manufacturing landscape is experiencing a digital revolution, and one of the most crucial areas impacted is safety.Gone are the days of relying solely on paper checklists and reactive incident response. Today, digital transformation in industrial safety is driving a wave of smart solutions, leveraging technologies like the Internet of Things (IoT) and data analytics to create a safer and more efficient work environment. Here’s what you should know how and why digital transformation is so critical to industrial manufacturing safety.
Why Embrace Digital Transformation for EHS in Manufacturing?
Traditional safety practices in manufacturing, while well-intentioned, often suffer from limitations. Reactive approaches to incident management can only do so much. Proactive measures, empowered by digital solutions, offer substantial advantages:
- Enhanced Real-Time Monitoring: Sensors embedded in machinery and equipment provide continuous data on performance, allowing for predictive maintenance and identifying potential issues before they lead to accidents.
- Improved Situational Awareness: Wearable technology can track worker location and vital signs, alerting supervisors to potential risks or providing critical information during emergencies.
- Data-Driven Safety Culture: Analytics help identify trends and patterns in safety incidents, enabling targeted interventions and customized training programs for at-risk areas or tasks.
- Optimized Safety Protocols: Automated systems can enforce safety procedures, such as machine lockouts during maintenance or access control to hazardous zones.
- Reduced Downtime and Costs: Predictive maintenance minimizes unplanned equipment failures, improving production efficiency and reducing associated costs.
Smart Solutions Leading the Way
Several key technologies are driving this digital transformation in industrial safety. Let’s delve deeper into some specific examples of smart solutions transforming industrial safety:
1. Predictive Maintenance
- IoT sensors embedded in machinery continuously monitor vibration, temperature, and other critical parameters.
- AI algorithms analyze this data to predict potential failures before they occur, allowing for timely maintenance interventions. This prevents unplanned downtime, reduces repair costs, and minimizes the risk of accidents caused by equipment malfunctions.
Example: A leading automotive manufacturer uses AI-powered predictive maintenance to analyze data from hundreds of sensors on their assembly robots. This has helped them reduce unplanned downtime by 20% and prevent several potential accidents by catching equipment issues early.
2. Wearable Technology
- Smartwatches or wristbands monitor worker location, vital signs, and exposure to environmental hazards.
- Real-time alerts notify supervisors of potential risks like fatigue, heat stress, or falls, enabling prompt intervention.
- Geofencing technology restricts access to hazardous zones based on individual worker permissions and real-time location data.
Example: A chemical processing plant equips its workers with wearable devices that track their location and exposure to dangerous chemicals. This system has helped them prevent several near misses by alerting supervisors when workers enter restricted areas or experience unsafe exposure levels.
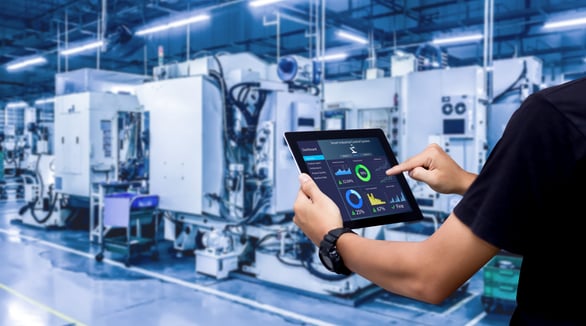
3. Digital Twins
- Virtual replicas of physical assets like production lines or entire factories are created in digital models.
- Simulations can be run on these digital twins to test safety procedures, identify potential hazards, and optimize workflow without disrupting actual operations. This allows for a proactive approach to safety, addressing potential issues before they occur in the real world.
Example: A large aerospace manufacturer uses digital twins to simulate different scenarios and test emergency response procedures for their complex assembly lines. This has helped them refine their safety protocols and ensure optimal response times in case of an incident.
4. Collaborative Robots (Cobots)
- These robots work alongside human workers, performing tasks that are repetitive, dangerous, or ergonomically challenging.
- Safety features like built-in sensors and pressure-sensitive limits prevent injuries to human workers if they come into contact with the robot. Cobots free up human workers for more complex tasks, reducing their exposure to repetitive and potentially hazardous activities.
Example: An automotive manufacturer uses cobots to handle heavy parts on their assembly line. This has reduced ergonomic risks for human workers and improved overall safety on the production floor.
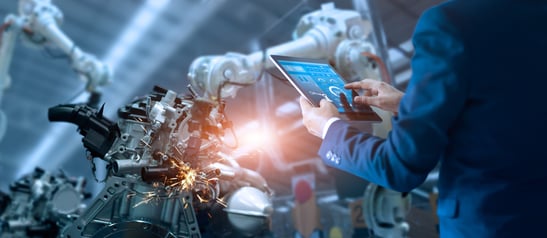
5. Blockchain for Data Integrity
- Blockchain technology can be used to securely store and share safety data across different departments and even with external partners.
- This ensures data integrity and transparency, allowing for more informed decision-making regarding safety protocols and incident investigations.
Example: A consortium of pharmaceutical companies is exploring the use of blockchain to securely share safety data related to their clinical trials. This collaboration allows them to identify potential safety risks more quickly and efficiently.
These are just a few examples of how smart solutions are transforming industrial safety. As technology continues to evolve, even more innovative applications will emerge, paving the way for a future where manufacturing facilities are not only efficient and productive, but also demonstrably safe for everyone involved.
Implementation Considerations
While the advantages of digital transformation for EHS in manufacturing are undeniable, successful implementation requires careful planning and thoughtful consideration of potential challenges and best practices. Let’s explore some key areas to address:
1. Data Security and Privacy
- Robust infrastructure: Implement robust cybersecurity measures to protect sensitive data collected from sensors, wearables, and other smart devices. Encrypt data at rest and in transit, regularly update security software, and conduct vulnerability assessments.
- Access control: Establish clear access control policies to ensure only authorized personnel can access and manipulate safety data. Implement multi-factor authentication and role-based access control mechanisms.
- Data anonymization: Consider anonymizing or pseudonymizing data, especially when it contains personally identifiable information about workers. This helps protect worker privacy while still enabling valuable safety insights.
- Transparency and trust: Communicate clearly with workers about how their data is collected, used, and protected. Building trust is essential for encouraging cooperation and adoption of new safety technologies.
2. Change Management
- Communication and engagement: Proactively communicate the benefits and goals of digital transformation for safety. Involve stakeholders across all levels in the decision-making and implementation process.
- Training and skills development: Provide comprehensive training for workers on using new technologies and understanding safety protocols within the digital framework. Equip them with the skills needed to effectively leverage these tools.
- Address concerns: Acknowledge and address worker concerns about job displacement, privacy, and potential misuse of technology. Provide reassurance and opportunities for feedback throughout the transition.
- Celebrate successes: Highlight and celebrate positive outcomes achieved through digital transformation in safety. This reinforces the value of the changes and motivates continued engagement.
3. Integration and Interoperability
- Evaluate existing systems: Analyze your existing IT infrastructure and identify potential roadblocks to integration with new technologies.
- Standardization: Consider adopting industry-standard data formats and communication protocols to ensure seamless integration between different devices and software platforms.
- Open API integration: Utilize open APIs (application programming interfaces) to facilitate data exchange between disparate systems and avoid vendor lock-in.
- Scalability: Choose solutions that can scale with your organization’s needs and accommodate future growth and integration of new technologies.
4. Investment and ROI
- Conduct a cost-benefit analysis: Carefully assess the upfront costs of implementing new technologies and compare them to the projected benefits in terms of improved safety, reduced downtime, and increased efficiency.
- Focus on long-term value: While initial investment may be substantial, consider the long-term return on investment (ROI) from improved safety performance, reduced accident costs, and increased productivity.
- Seek funding opportunities: Explore grants, tax incentives, and partnerships with technology providers to help offset the cost of implementation.
- Measure and track progress: Continuously monitor the impact of your digital transformation efforts on safety metrics, productivity, and overall ROI. Use data to refine your approach and demonstrate the value of the investment.
Remember, navigating the road to digital transformation in industrial safety is an ongoing journey. By addressing these key considerations, ensuring ethical data practices, and prioritizing communication and worker engagement, you can successfully leverage smart solutions to create a safer, more efficient, and sustainable work environment for your manufacturing operations.
The Future of Industrial Safety is Smart
The industrial landscape is experiencing a transformative shift, and safety practices are no exception. By embracing digital transformation, manufacturers are unlocking a smarter, more proactive approach to safety, leveraging the power of IoT, AI, data analytics, and collaborative technologies.
As we look towards the future, here are some key trends shaping the evolution of industrial safety:
- Hyper-personalization: Safety solutions will become increasingly personalized, tailoring interventions and training to individual worker needs and risk profiles, further enhancing effectiveness.
- Human-Robot Collaboration: Collaborative robots (cobots) will seamlessly integrate into workflows, taking on hazardous tasks while empowering human workers to focus on higher-level cognitive activities.
- Immersive Technologies: Virtual reality (VR) and augmented reality (AR) will revolutionize training, enabling workers to practice real-world scenarios in a safe and controlled environment.
- Predictive and Prescriptive Safety: AI-powered systems will not only predict potential risks but also prescribe corrective actions, creating a truly proactive approach to preventing accidents.
- Decentralized Intelligence: Safety intelligence will move beyond centralized control rooms, residing closer to the edge in devices and wearables, enabling real-time decision-making at the operational level.
- Closed-Loop Safety Systems: Data will flow seamlessly between different systems, creating a closed-loop feedback system that continuously learns and improves safety protocols based on real-world data.
- Collaborative Ecosystem: Manufacturers will increasingly collaborate with technology providers, researchers, and regulatory bodies to share best practices, develop innovative solutions, and accelerate the overall progress of safety advancements.
Embracing these trends requires a collaborative effort from all stakeholders. Manufacturers must invest in technology, upskill their workforce, and prioritize data security and ethical practices. Technology providers need to develop user-centric solutions that integrate seamlessly and address real-world challenges. Governments and regulatory bodies should create frameworks that encourage innovation while ensuring responsible use of technology.
Ultimately, the future of industrial safety is not just about smarter technology, but about smarter partnerships and a shared commitment to creating a safer work environment for everyone. By working together, we can leverage the power of digital transformation to unlock a future where accidents are not just reduced but prevented entirely, paving the way for a more sustainable and prosperous manufacturing industry.
