If any manufacturing company wants to succeed in the long run, they need to be able to master good manufacturing practices (GMP). Of course, the GMP process is long and complex, which means it’s not easy to master. Mistakes are bound to be made along the way.The key is to understand some of the shortcomings and GMP violations that other businesses make so that those areas can receive special attention. That’s why we wanted to mention some of the common GMP shortcomings to help manufacturing companies stay ahead of the curve.
Failure to Test
In manufacturing, everything needs to be regularly tested. This doesn’t just mean quality control inspections for the end product. Procedures, machinery, equipment, and everything else should be tested regularly as well. In short, every part of the process requires testing to make sure it’s performing at optimal levels.
Regular testing not only ensures efficiency but also helps in identifying potential issues before they escalate into major problems. By catching these issues early, companies can save time and resources, ultimately leading to a more streamlined and cost-effective production process.
Using the Wrong Equipment
Too many companies use the wrong equipment for certain tasks without even realizing it. This is why testing everything is a critical part of good manufacturing practices. In some cases, equipment is outdated while in other cases employees are using equipment the wrong way. Both of these are elements that should be monitored and checked regularly. Additionally, investing in employee training can significantly reduce the misuse of equipment.
By ensuring that staff are well-versed in the latest technologies and techniques, companies can enhance productivity and minimize the risk of equipment-related errors. This proactive approach not only safeguards the machinery but also empowers employees to perform their tasks more efficiently.
Not Inspecting Raw Materials
In most cases, a business can only be as successful as the raw materials it uses. This is why raw material inspections should be conducted with every shipment. If the raw materials aren’t up to certain standards, there’s no way the end product can meet certain standards. Therefore, it’s good practice to always make sure raw materials are thoroughly inspected every time.
Consistent inspections help in building strong relationships with suppliers. By maintaining open communication and setting clear expectations, companies can ensure that suppliers understand the quality requirements and are committed to meeting them. This collaboration not only enhances the quality of the raw materials but also fosters a reliable supply chain, which is crucial for maintaining production schedules and meeting customer demands.
Lack of Sanitation
Cleanliness is a key ingredient in any workplace, although it’s particularly important in manufacturing. Clean workspaces look more professional and tend to function with more efficiency. Also, the quality of some products can be threatened by unkempt work environments or employees who aren’t taking personal hygiene seriously.
Maintaining a high standard of cleanliness can significantly reduce the risk of contamination, which is crucial in industries such as food production and pharmaceuticals. Regular cleaning schedules and strict hygiene protocols not only protect the integrity of the products but also ensure compliance with health and safety regulations. By prioritizing cleanliness, companies can foster a culture of responsibility and care, ultimately leading to higher employee morale and customer satisfaction.
Poor Record Keeping
One of the best manufacturing practices is to keep records of everything. As the old saying goes, knowledge is power. One of the best ways for a company to acquire knowledge is to document everything that happens. This means all parts of the manufacturing process from beginning to end are closely monitored and recorded. This can help give meaningful insight to company leaders, giving them as much information as possible when it’s time to make important decisions about the business.
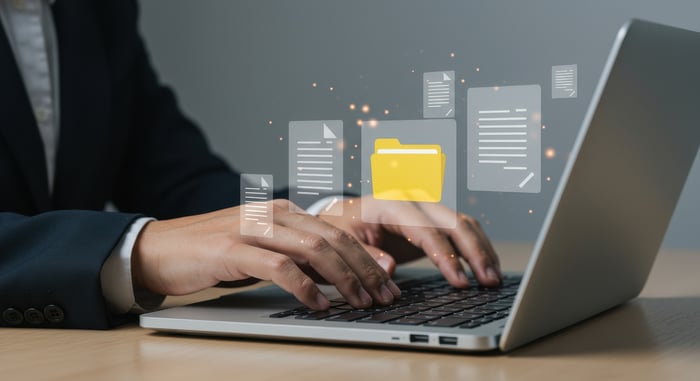
Comprehensive record-keeping can also serve as a valuable tool for training new employees. By having detailed documentation of past processes and decisions, new staff members can quickly get up to speed and understand the company's operations more thoroughly. This not only accelerates the onboarding process but also ensures that new employees are aligned with the company's standards and practices from the outset.
Not Enough Self Audits
In case it’s not been made clear by the other items on this list, the best manufacturing practices usually involve being proactive. Companies should be encouraged to conduct regular self-audits that take a close look at all company practices. This can include employees from within the company taking a deep dive into company practices or hiring a fresh set of eyes from outside the company to inspect things. Either way, self-examination is a critical part of understanding the strengths and weaknesses of a business and finding a way to improve operations. After all, good manufacturing practices should always be considered a work in progress. Self auditing can foster a culture of continuous improvement and innovation.
By regularly assessing their processes, companies can identify areas where they can implement new technologies or methodologies to enhance efficiency and productivity. This ongoing commitment to improvement not only helps in maintaining high standards but also positions the company as a leader in the industry, ready to adapt to changing market demands and technological advancements
Not Taking Employee Safety Seriously
Typically, the best manufacturing companies are often the safest companies. The businesses that pay the most attention to employee health and safety are usually diligent in other areas. If safety is a priority, we recommend the safety management software from EHS Insight. We have created a system that carefully monitors all aspects of occupational safety in a way that streamlines the entire process. Not only does it lead to a safer work environment but it can also help to cut costs in the long run because of the accidents that can be avoided.
If your company wants to get ahead when it comes to workplace safety, let’s chat about how our software can help you maintain a safe working environment for everyone.
